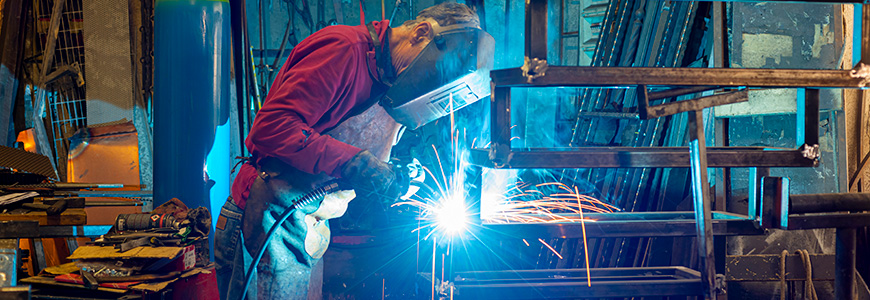
Ever wonder how raw metal from the earth gets transformed into that beautifully shaped, polished and shining piece of jewelry gracing your finger, ear, neck or wrist? Blacksmithing, a craft as old as civilization itself, is the answer. It's not just about shaping steel with heavy hammers and roaring forges, though that's certainly part of it! It's also about the delicate art of morphing precious metals into intricate forms, using heat, tools and a deep understanding of how each material reacts. Whether you're picturing a sturdy tool forged from steel or a delicate silver ring, the core techniques—forging, heat treating, and welding—remain the same. Dive into the fiery world of blacksmithing terms and unlock the secrets behind transforming plain metal into beautiful masterpieces.
Blacksmith Tool Terms
Since blacksmiths often heat metal dangerously high to hammer and shape it into fine jewelry (or any other type of metalwork), they need some tools (and, more importantly, some knowledge about what those tools do and how to use them!) first! (NOTE: It's best to leave the blacksmithing to the blacksmiths. Plus, getting your ring resized can often be pretty affordable, as long as drastic changes aren’t required.) Here are some of the tools commonly used in blacksmithing:
Forge
A blacksmithing forge is a powerful hearth where metal is transformed by intense heat. More than just a simple fire in a fireplace, it's a carefully controlled high-heat environment designed to bring metal to its working temperature. Traditionally, forges used coal or charcoal, fueled by a bellows (hand-cranked blower). Modern blacksmiths often utilize gas forges, offering precise temperature control and a cleaner burn.
Regardless of the fuel, the forge's ability to concentrate heat is the key to this craft. This allows the blacksmith to manipulate the metal's properties, making it malleable for shaping, welding and heat treating. This crucial tool is the key to creating everything from rugged tools and intricate ironwork to delicate jewelry pieces.
Anvil
In blacksmithing, an anvil is a heavy, firmly secured, steel-surfaced block where the piece of iron is worked. Several anvil types are used, depending on the type of metalwork being done.
Jeweler's anvils
In jewelry making, a smaller, often highly polished anvil serves as a stable and precise surface for hammering, shaping and texturing precious metals during the blacksmithing process.
Blacksmith anvils
The most common anvil, the blacksmith anvil is both versatile and robust, with a large face and a horn.
Farrier anvils
Tailored for shaping horseshoes, this anvil has a narrower face and specialized horns.
Bench anvils
Compact and lightweight, this anvil is ideal for fine, detailed work and precision.
Stake anvils
This portable anvil has a spiked base for secure mounting.
Double horn anvils
These anvils offer maximum versatility with two horns, as the name suggests, for different shaping options.
Hammer
Blacksmithing hammers (as well as other tools like chisels) are used to cut, shape, flatten or weld metal into its desired shape. Blacksmithing hammers vary in shape and weight to perform specific tasks. Jewelry making utilizes smaller, specialized hammers, often with polished faces, to precisely shape and texture precious metals on the anvil, providing controlled force for delicate work. Hammering may also be used to resize a ring, especially those with thicker bands. This requires careful and even hammering to maintain the ring's shape.
Tongs
Blacksmiths use tongs to hold the iron on the anvil during the hammering and shaping process, providing a safe and secure grip while working with hot metal. These essential tools come in various shapes and sizes, each designed for specific tasks, from holding flat stock (metal in flat bars, sheets or plates) to gripping round bars. In the more delicate realm of jewelry making, specialized tongs are used to maintain a controlled grip. These tongs are often smaller, more delicate and meticulously designed to grip and manipulate fine wires, small components and precious metals with precision, minimizing damage and allowing for intricate work.
Blacksmithing Process and Technique Terms
Shaping and transforming metal takes more than just smashing hammers against giant chunks of metal. There are specific, skill-intensive processes and techniques that are learned and used to create the strong and beautiful pieces we know.
Forging
Forging is the heart of blacksmithing, a process where metal is transformed through controlled heating and hammering. Blacksmiths heat the metal until it's malleable, then use hammers and anvils to shape it into desired forms. This technique allows for the creation of durable tools, intricate designs and functional objects.
Heat Treatment
This involves controlled heating and cooling of metal to alter its physical and mechanical properties. It's crucial for achieving the desired hardness, toughness, and durability. Here are a few popular heat treatments.
Annealing
This blacksmithing term refers to the process of heating metal up and then slowly cooling it to soften it. In jewelry making, annealing is crucial for softening precious metals like silver and gold after they've rehardened during the forming process, allowing for further delicate shaping and intricate detailing without cracking.
Quenching
Quenching includes rapidly cooling heated metal, usually in water or oil, to increase its hardness. When making jewelry, blacksmith quenching is used to harden and strengthen materials like steel, copper, silver and gold by immersing them in a liquid like water or oil after heating.
Tempering
Tempering is the reheating of quenched metal to a lower temperature to reduce brittleness and increase toughness. In jewelry blacksmithing, tempering is primarily used to ensure the durability and longevity of delicate components, especially those that require flexibility or resistance to bending, like clasps, springs and certain types of wire work.
Welding
Welding is the process of combining two pieces of metal by heating and fusing them. Essential for joining jewelry components, welding techniques like soldering or laser welding create seamless bonds between precious metal pieces, forming intricate designs and secure settings.
Forge Welding
Forge welding involves heating two pieces of iron or steel to a very high temperature and hammering them together to create a bond. Though less frequently employed in fine jewelry, forge welding principles can be seen in creating patterned or laminated metal for unique jewelry elements, where different metals are fused through heat and hammering.
Arc Welding
Arc welding uses an electric arc (a sustained electrical discharge between two electrodes through an ionized gas, producing intense heat) to melt and fuse the metal pieces together. Arc welding is used in jewelry to create strong, precise joins, especially for larger or more structural pieces such as a heavy clasp.
Common Blacksmithing Material Terms
Blacksmithing techniques are adapted for jewelry making to create unique and handcrafted pieces. Precious metals like sterling silver and gold, prized for their malleability and beauty, are shaped using similar hammering and heating methods. Copper and brass, often chosen for their warm tones and affordability, allow for intricate designs and textured surfaces. While less common, steel can add a rustic or industrial aesthetic to jewelry. The selection of metal directly influences the jewelry's final appearance, durability and the level of detail achievable.
Types of Metals
But because blacksmithing isn’t only about jewelry, here are some of the most common metals used in blacksmithing overall.
Mild steel
A versatile and affordable option, mild steel is known for its workability and ability to be hardened through heat treatment. A hammer is an example.
High-carbon steel
High-carbon steel requires careful heat treatment for optimal hardness and is ideal for creating durable tools and blades. A chef's knife, a woodworking chisel or a durable sword blade are examples of things created from high-carbon steel.
Wrought iron
Historically significant, wrought iron is valued for its fibrous texture and ease of forging, and it is often used for decorative ironwork. Traditional wrought iron gates, anyone?
Copper
A malleable and conductive metal, copper is favored for its warm tones and ability to be shaped into intricate designs. Copper boasts a wide range, from delicate jewelry pendants to electrical components.
Brass
An alloy of copper and zinc, brass offers a golden hue and good workability, making it suitable for decorative and functional pieces. Another versatile metal; one day, it’s forging furniture hardware; the next, it’s a set of percussion bells!
Not all metal types are ideal for blacksmithing. For example, certain alloys, such as white gold, are harder, requiring higher heat and making them more difficult to shape than other metals.
Blacksmithing Fuel Source Terms
The heart of any blacksmithing endeavor lies in the forge, where the fuel source dictates the heat, control, and character of the work. Choosing the right fuel, whether charcoal, coal or gas, is a fundamental decision that shapes the entire crafting process.
Charcoal
A lightweight and relatively clean-burning fuel, charcoal produces a consistent heat ideal for delicate work and smaller forges.
Coal
A dense and high-energy fuel, coal generates intense heat suitable for heavy forging and large-scale projects but produces more smoke and requires careful management.
Gas
A convenient and easily controlled fuel source, gas-fueled forges offer consistent heat and reduce smoke, making them popular for modern blacksmithing. Gas forges are generally preferred when blacksmithing jewelry due to their precise temperature control, clean burning and ability to maintain consistent heat, which is essential for working with delicate and precious metals.
Protect your Blacksmithing Work of Art
If you have well-crafted jewelry, consider protecting it with a personal jewelry insurance policy from Jewelers Mutual. Although crafting your piece likely took hours in a forge, getting a personal jewelry insurance quote online takes just a few minutes. Click the link below to ensure your pieces are protected today!